Glass Reactor
UD Technologies are Leading manufacturers and exporters of Glass reactor, jacketed glass Reactor, Filter reactor from Vadodara, Gujarat, India .
We manufacture Glass Reactor with the highest quality standards of workmanship and material.
The Reactor is a vessel or system in which chemical Reaction proceeds and Reactants converts in Production.Design of Chemical Reactor Varies Widely with process Parameters.
Due to transparency and Universal Corrosion resistance;Chemist s and Process Engineers prefers Borosilicate Glass for Kilo lab, Pilot plants and Production for small batches.
Cylindrical Shape widely uses considering Geometric and Kinematic Similarity with Commercial Reactors.
Appropriate design of Glass Chemical Reactor is crucial for Pilot plant trial success.UD Technologies offers several solutions to select appropprite Glass Reactor .
There are two main variants :Batch reactor and continuous reactor .Semi Batch or semi Continuous reactor is also suitable for certain Chemical Reactions .
We offer different types of Glass Reactor which is widely used in Industry and Process Engineers has exact Option considering process requirement
A.Glass Batch Reactor
A2.Trippled Wall Reactor
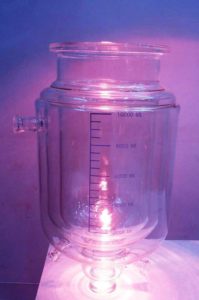
A3. Glass Photo Reactor
A4. Glass Filter Reactor
B.Glass Continuous Stirred tank Reactor (CSTR)
Glass Continuous Stirred Tank Reactor is widely used for Instantaneous reaction or with lower residence time.For Higher residence time,Multiple CSTR in series used.
C.Glass Plug Flow Reactor (PFR)
C.1. Glass Tubular Plug Flow Reactor
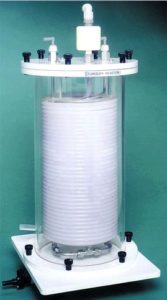
C2. Glass Falling Film Reactor
Falling film reactors display outstanding heat removal capability, with the mix between reagents leading to milder reaction conditions than in stirred batch reactors.
D.Glass Semi Batch Reactor
Glass Semi Batch Reactor or Semi Continuous reactor is reactor where some of Raw materials and Products continuously added or Removed
Please visit following links for more products and Information
Scale Down Study in Glass Reactor
[/vc_column_text]