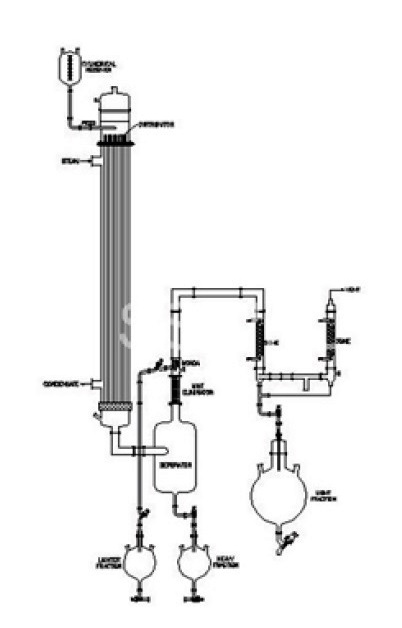
Falling Film Evaporator
Buy High-Efficiency Glass falling-film-evaporator– UD Technologies
Looking for a high-performance falling-film-evaporator in borosilicate Glass and PTFE for Heat sensitive and corrosion resistant liquids ? The falling-film-evaporator in Borosilicate Glass and PTFE by UD Technologies delivers exceptional results in concentration, distillation, and solvent recovery — all with full visibility and precise control.
🌟 Why Choose UD Technologies’ falling-film-evaporator?
Looking to optimize your evaporation process with high efficiency and visibility? The Glass falling-film-evaporator from UD Technologies is a top choice for R&D labs, pilot plants, and specialized chemical industries.
Why Choose Our falling-film-evaporator?
- ✅ Crystal Clear Operation – See your process live with full glass visibility.
- ✅ Engineered for Performance – Rapid heat transfer with reduced product hold-up.
- ✅ Protects Heat-Sensitive Products – Achieve concentration without compromising quality.
- ✅ Custom-Built Designs – Tailored configurations for your exact process needs.
- ✅ Compact and Scalable – Start from pilot to production with consistent technology.
Industries Benefiting from Our Evaporator
- Life Sciences & Pharmaceuticals
- Food Processing & Extracts
- Herbal, Ayurvedic & Nutraceuticals
- Fine & Specialty Chemicals
- Contract Research and Testing Labs
Boost Efficiency. Improve Yields. Cut Solvent Costs.
Whether you’re developing new formulations or scaling up a sensitive process, UD Technologies’ Glass Falling Film Evaporator provides unmatched control, visibility, and reliability.
Size and Available Models
Are available in Heat transfer area from 2 Sq. Mt to 20 Sq. Mt. and From Diameter 4” to 12”.Larger sizes can be offered on request
Principle of Operation:
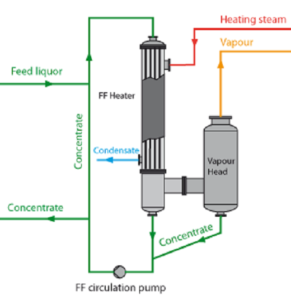
In falling film evaporators, liquid and vapors flow downwards in parallel flow. The liquid to be concentrated is preheated to boiling temperature if required. An even thin film enters the heating tubes via a distribution device in the head of the evaporator, flows downward at boiling temperature, and is partially evaporated.
The liquid to be evaporated is evenly distributed on the inner surface of a Glass tube. The liquid will flow downwards forming a thin film, from which the boiling/evaporation will take place because of the heat applied by the hot oil . . A number of tubes are built together side by side. At each end the tubes are fixed to tube plates, and finally the tube bundle is enclosed by a shell made either of steel or Glass depending upon the Hot oil pressure. The Hot oil is introduced through the shell. The space between the tubes is thus forming the heating section. The inner side of the glass tubes is called the boiling section. The concentrated liquid and the vapor leave the evaporator at the bottom part, enters the subsequent separator tangentially from where the concentrated liquid is discharged (usually by means of the pump) from the bottom and vapor leave the separator from top.
Advantages
Glass falling-film-evaporator can be operated with very low temperature differences between the heating media and the boiling liquid, and they also have very short product contact times, typically just a few seconds per pass. These characteristics make the falling film evaporator particularly suitable for heat-sensitive products, and it is today the most frequently used type of evaporator.
However, falling film evaporators are designed very carefully for each operating condition; sufficient wetting of the heating surface by liquid is extremely important for trouble-free operation of the plant. If the heating surfaces are not wetted sufficiently, dry patches and incrustations will occur; at worst, the heating tubes will be completely clogged.
Critical Design
The proper design of the liquid distribution system is critical to achieve full and even product wetting of the tubes. This is specially designed by ‘UD Technologies’.
Because of the low liquid holding volume in this type of unit, the falling film evaporator can be started up quickly and changed to cleaning mode or another product easily.
Falling film evaporators are highly responsive to alterations of parameters such as energy supply; vacuum, feed rate, concentrations, etc. When equipped with a well-designed automatic control system ,they can produce a very consistent concentrated product.
Selection Criteria referring to Vapor exit location
Flow of vapor and liquid may be either co-current, in which case vapor-liquid separation takes place at the bottom, or countercurrent (the liquid is withdrawn from the bottom and the vapor from the top). For co-current flow, the vapor shear-forces thin the liquid film, and yield higher heat-transfer coefficients. Moreover, since the vapor is in contact with the hottest liquid at the point of withdrawal, stripping is more efficient.
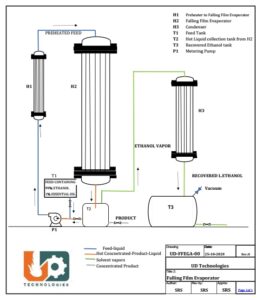
In countercurrent flow, shear forces increase the liquid-film thickness, and reduce the heat-transfer coefficient. If the vapor flow rate is high enough, it may lead to flooding of the tubes, with liquid carried upward beyond the point of injection, resulting in decreased performance and unstable operation. Countercurrent operation is used where it is necessary to evaporate a liquid at a low temperature under vacuum conditions, or where an inert gas (e.g., nitrogen or air) is injected into the tubes at the bottom of the unit to reduce the partial vapor pressure, and hence boiling point, of the liquid.
📞 Contact us today on +91-7990397491 (Whatsapp) or [email protected] for a customized solution
For other Options of Gentle Evaporation of Heat Sensitive solution
Large Scale Rotary Film Evaporator
Useful Information